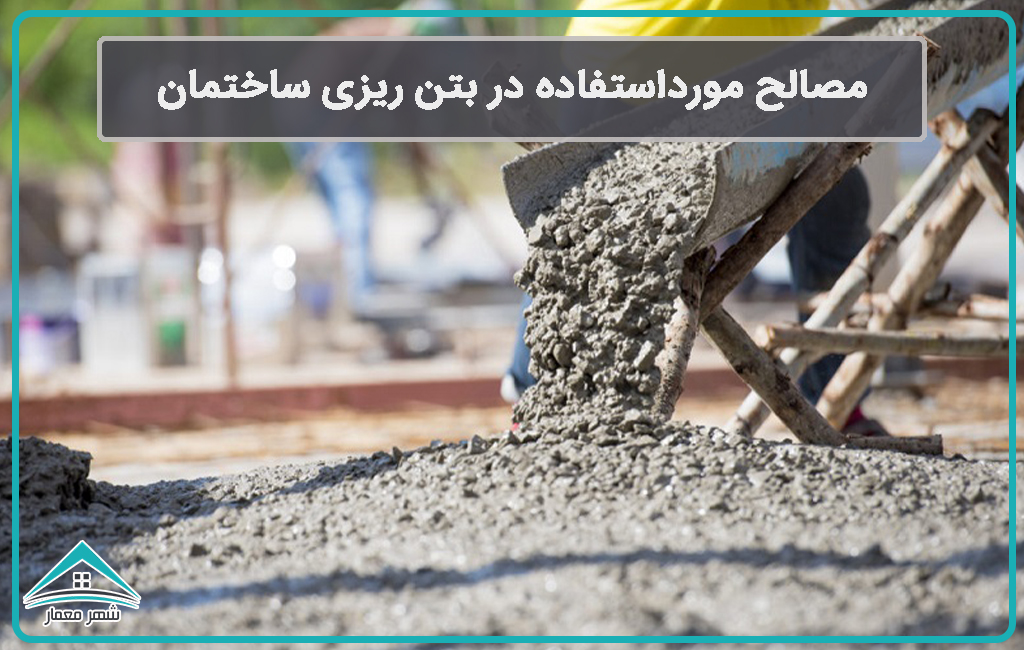
مواد تشکیلدهنده بتن در بتن ریزی
بتن ماده کامپوزیتی متشکل از یک چسب بوده که معمولاً سنگ، ماسه و آب هستند. این مواد تشکیلدهنده بتن برای بتن ریزی است؛ اما به دلیل متغیرهای فراوان مواد اولیه، نحوه پردازش و ترکیب آنها، فرصتهای زیادی برای ظهور مشکلات در بتن وجود دارد. داشتن درک بنیادی از مواد مختلف و فرآیندهای تولید ممکن است به کسانی که بتن را بازرسی میکنند، کمک کند تا بدانند چه مشکلاتی را کجا جستجو کنند و چگونه آنها را تشخیص دهند. در ادامه شما را با انواع مصالح مورداستفاده در بتن ریزی آشنا می کنیم.
مواد تشکیلدهنده بتن در بتن ریزی به زبان ساده
سیمان + آب = خمیر سیمان
خمیر سیمان + ماسه = ملات
ملات + سنگ = بتن
مواد افزودنی ممکن است برای کنترل خصوصیات تنظیمات، در مخلوط موجود باشد. واکنشهای شیمیایی که هنگام ترکیب مواد سازنده مختلف اتفاق میافتد، بسته به خصوصیات مواد منفرد متفاوت است. این مواد بسته به محل استخراج یا استخراج آنها و با توجه به روشهای ساخت و شرایط استفادهشده در کارخانه تولید بتن ریزی، میتوانند ازنظر ترکیبات شیمیایی و خصوصیات عملکردی آنها متفاوت باشند.
منظور از بایندر در بتن ریزی چیست؟
بایندر مواد ریز و دانهای هستند که وقتی آب به آنها اضافه میشود بهصورت خمیر درمیآیند. این خمیر، سنگدانهها و فولاد تقویتکننده را سخت و محصور میکند. بلافاصله پس از افزودن آب، خمیر سیمان از طریق یک فرآیند شیمیایی به نام هیدراتاسیون شروع به سخت شدن میکند.
هیدراتاسیون با توجه به خصوصیات مختلف اتصالدهندهها و مواد افزودنی استفادهشده، نسبت آب به سیمان و شرایط محیطی که بتن در آن قرار میگیرد، با سرعتهای مختلف انجام میشود. روشهایی که مواد چسبنده روی بتن، ملات و محصولات مشابه تأثیر میگذارد، میتواند ازنظر خصوصیات شیمیایی و فیزیکی مواد منشأ، مواد تشکیلدهنده، طرح مخلوط در فرآیند تولید سیمان متفاوت باشد.
ترکیبات مهم سیمان پورتلند
سیمان انواع مختلفی دارد اما سیمان پرتلند چسبانندهای است که بهطور گسترده استفاده میشود. سیمان پرتلند به دلیل منطقهای در انگلیس که استفاده از آن آغازشده، نامگذاری شده است، اما امروزه در سراسر جهان تولید میشود.
سیمان پرتلند از ترکیب مواد حامل کلسیم با مواد حاوی آلومینیوم ساخته میشود. کلسیم ممکن است از سنگآهک، پوسته، گچ یا مارن حاصل شود. مارن یک سنگ نرم یا گل سفت است که گاهی اوقات گل ماسه نامیده میشود و غنی از آهک است.
فرآیند کامل تولید سیمان برای بتن ریزی
عملیات اساسی کارخانههای سیمان تقریباً مشابه بوده اما ممکن است بسته به مکان متفاوت باشد. فرآیند تولیدی که در زیر میآید، آنچه در معادن سنگ و کارخانه سیمان اتفاق میافتد را شرح میدهد.
عملیات معدن برای تولید سیمان
- یکلایه سطحی آهک به ضخامت حدود ۱۸ فوت را میشکند و در زیرزمین قرار میگیرد. عملیات معدن کاری قبل از اینکه دیگر سودآوری نداشته باشد، آن را تا حدود ۲۰۰ فوت دنبال میکند.
- سنگ تیرهرنگ که حاوی سنگآهک و دو نوع شیل است، که از همه آنها در تولید سیمان برای بتن ریزی استفاده میشود. مواد رنگ روشن را که بار مینامند، در ساخت استفاده نمیشوند، آنها کنار گذاشتهشده تا بعد از پایان کار و تعطیل شدن معادن، در هنگام احیا جایگزین شوند.
- ناحیه مسطح در دیواره معدن که به آن بالابر یا نیمکت گفته میشود، عمقی است که قبل از تنظیم بار برای انفجار، سوراخهایی (حدود ۸۰ فوت) در آن ایجاد میشود. به دلیل الزامات امنیتی، بیشتر معادن عملیات انفجار را از قرارداد خارج میکنند.
- پس از انفجار، سنگ زباله به انتهای معدن که در آنجا معدن کاری برای اولین بار آغازشده، آورده میشود. این اولین مادهای خواهد بود که بهعنوان بخشی از فرآیند احیای مجدد پر میشود. سنگ قابلاستفاده توسط کامیون حمل شده و یا در سنگشکن اولیه ریخته و یا در نزدیکی آن انباشته میشود.
- جادهها و تیر پایهها باید آبیاری شوند تا گردوغبار موجود در هوا کاهش یابد.
- کامیونها دوباره به داخل این ساختمان وارد میشوند تا بارهای خود را به سنگشکن اولیه بریزند.
نقش فیلتر در عملیات معدن
- بعدازاینکه سنگ از بالا به ناودان خوراک ریخته شد، جاذبه آن را از طریق سنگشکن به پایین منتقل میکند و قطر آن را به حدود ۳ اینچ کاهش میدهد. فیلتر کیسه به کاهش گردوغبار موجود در هوا کمک میکند.
- از سنگشکن، سنگبر روی یک تسمهنقاله حرکت کرده که آن را به کارخانه تولید حدود ۲ مایل دورتر است، منتقل میکند.
- تسمههای نقاله بلند باید با کشش مناسب تنظیم شوند. این کار با استفاده از کابلهای فولادی برای تعلیق وزن بتن در داخل برجها انجام میشود.
- در هر نقطه که نوار نقاله ارتفاع یا جهت خود را تغییر میدهد، فیلتر به پاک شدن گردوغبار حاصل از سنگ خردشده در هوا کمک میکند.
- سنگآهک و شیل سرانجام در انتهای خط تولید، انبار میشوند.
- سنگ با یک لودر جلویی هر بار توسط یک سطل روی نوار نقالهای که آن را به داخل سیلوی موج، حمل میکند، بارگیری میشود. از سیلو ولتاژ میتوان سنگ را با سرعت یکنواخت به سیستم منتقل کرد. سنگ از سیلوی موج به خشککن منتقل میشود که بیشتر رطوبت را از بین میبرد و قبل از بازگشت به دستگاه خردکن ثانویه (سیلوی مرکزی)، جایی که قطر آن به حدود ۳/۸ اینچ کاهش مییابد. از این نقطه، سنگ بهجای کمربندهای نگهدارنده غلتک، توسط هوا سریعالسیر حمل میشود.
- سپس سنگ خردشده به آسیاب گلولهای منتقل میشود که در آن گلولههای فولادی افتاده، آن را به یک پودر تبدیل میکنند. آسیاب توپی استوانهای در حال چرخش است که دارای یک پوشش بوده و توسط صدها پیچ در محل خود نگهداشته شده است. مواد مختلفی در آسیاب گلولهای ترکیب میشوند، بنابراین در اینجا محل اختلاط اولیه است. مواد معمول عبارتاند از؛ سنگآهک، شیل، ماسهسنگ و آهن.
- از آسیاب توپی، مواد قبل از گرمادهی به برج منتقلشده، جایی که قبل از انتقال به کوره افقی، استوانهای و چرخشی تا حدود ۱۸۰۰ درجه فارنهایت گرم میشود.
منظور از فرایند پخت در تولید سیمان برای بتن ریزی چیست؟
- کوره (خاکستری تیره) کمی کج شده، بهطوریکه مواد هنگام چرخش از طریق آن حرکت میکند. لوله با شیب بیشتر روی کوره (خاکستری روشن) هوای احتراق را تأمین کرده، همانطور که مجرای U شکل در بالای برج قبل از گرما نیز وجود دارد. در داخل کوره، مواد تا حدود ۳۳۰۰ درجه فارنهایت گرم شده، به این فرآیند، پخت گفته میشود. تغییرات شیمیایی رخ میدهد که منجر به تشکیل مادهای بهاندازه سنگ مرمر به نام کلینکر میشود. ایجاد کلینکر به معنای استفاده از گرما برای بیرون راندن کل دیاکسید کربن از مواد بوده و دیاکسید کربن یکی از گازهای اصلی گلخانهای است.
- عکس بالا درب های باز را در انتهای پایین کوره نشان میدهد که برای بازرسی و سرویسدهی بسته میشوند. لوله انعطافپذیر به قطر ۶ اینچ که به سمت چپ متمایل است، منبع سوخت مشعل بوده که باعث سوختن زغالسنگ پودر میشود. انتهای لوله تأمین زغالسنگ ۸ اینچی درست در سمت راستپای کارگر وجود دارد.
- انبارهای زغالسنگ پودر شده برای سوختگیری کوره استفاده میشوند.
- کلینکر برای کنترل میزان رطوبت به یک انبار ذخیرهسازی با شکل خاص منتقل میشود.
- کلینکر، ریز خردشده و محصول نهایی سیمان را ایجاد میکند.
- کل عملیات از طریق یک کنسول کنترل مرکزی، کنترل میشود که شامل؛ نمایشگرهای متعددی با بازخوانی دیجیتال در زمان واقعی است.
عوامل مؤثر بر تغییرات عملکرد
اگرچه استانداردهای ASTM وجود دارد که سیمان پرتلند ممکن است با آنها مطابقت داشته باشد، تعدادی از عوامل وجود دارد که میتواند ویژگیهای عملکرد آن را تغییر دهد.
اندازه ذرات و تاثیر آن بر عملکرد
اندازه ذرات ازاینجهت مهم است که ذراتی که باظرافت بیشتری خرد میشوند، سطح بیشتری را ارائه میدهند که واکنشهای شیمیایی در برابر آنها اتفاق میافتد و اینها بهشدت بر خواص سیمان تأثیر میگذارند. سیمان با ذرات ریز واکنش بیشتری نشان میدهد و زودتر پس از شروع فرآیند هیدراتاسیون قدرت میگیرد. سطح کل ذرات در حجم معینی از مواد را سطح خاص آن مینامند. سیمانهای پرتلند دارای یک سطح خاص ۱۵۰۰ تا ۲۰۰۰ فوت مربع در هر پوند ماده (ft2 / lb)، برابر با حدود ۳۰۰ تا ۴۰۰ مترمربع در هر کیلوگرم (بسته به نوع) است.
تاثیر گچ و سولفاتها بر تغییرات
گچ، به شکل ذرات ریز، با کلینکر مخلوط میشود تا روند هیدراتاسیون بهاندازه کافی کند شود و زمان لازم برای قرار دادن بتن، ساییده شدن آن و پایان کار آن قبل از قرار گرفتن وجود داشته باشد. اگر مواد گچ یا سولفات به مواد کلینکر اضافه و آسیاب شوند، ممکن است اندازه آنها سریعتر از کلینکر کوچک شود.
این سنگزنی ترجیحی میتواند ذرات کوچکتری ایجاد کند که نسبت واکنش آنها در مقایسه با ماده کلینکر را افزایش دهد. برای هر سیمان خاص، محتوای بهینه، برای گچ و سولفات وجود دارد. جزئیات دقیق نحوه تأثیر سولفاتها بر مقاومت بتن بهخوبی مشخص نشده است.
موارد مؤثر بر محتوای مطلوب گچ و سولفات
محتوای مطلوب گچ و سولفاتها نهتنها به نوع مخلوط طراحی سیمان برای بتن ریزی بلکه به موارد زیر بستگی دارد:
- خواص شیمیایی مواد کلسیم و آلومینیوم مورداستفاده برای کلینکر
- خصوصیات فیزیکی آلومینات ها، مانند اندازه بلور
- حلالیت متفاوت منابع مختلف سولفاتها
- اندازه ذرات
- دمای فرز
- استفاده از مواد افزودنی
علت تولید انواع مختلف سیمان چیست؟
به نظر میرسد که این موضوع بهاندازه کافی پیچیده نباشد. محتوای بهینه سولفات برای یک خاصیت سیمان، مانند مقاومت، ممکن است با محتوای مطلوب برای خاصیت دیگر مانند، انقباض خشک شدن متفاوت باشد. بتن و ملات میتوانند محتوای مطلوب متفاوتی داشته باشند، به همین دلیل انواع مختلف سیمان تولید میشود.
در تلاش برای جلوگیری از بروز چنین مشکلاتی، در طی مراحل ساخت، چهار بار مواد آزمایش میشوند.
۱. مواد اولیه قبل از ورود به فرآیند تولید ۲. قبل از ورود به کوره ۳. پس از خروج از کوره ۴. قبل از ذخیره نهایی در سیلوهای ذخیره اصلی آزمایش میشوند.
۸ نوع سیمان پرتلند برای بتن ریزی
ASTM مشخصات C-150 استانداردهایی را برای هشت نوع مختلف سیمان پرتلند برای بتن ریزی فراهم میکند:
- نوع I: یک سیمان با کاربرد عمومی است که در طیف گستردهای از انواع پروژهها ازجمله؛ ساختمانها، پلها، کف، روسازی و پروژههای بتنی پیشساخته استفاده میشود.
- نوع IA: مشابه نوع I است اما برای بتن ریزی پروژههایی که نیاز به حفره هوادارند استفاده میشود.
- نوع II: گرمای کمتری و با سرعت کمتری گرما تولید میکند و مقاومت متوسطی در برابر حمله سولفات دارد.
- نوع IIA: با نوع II یکسان است اما برای بتن ریزی پروژههایی که به حفره هوا احتیاج دارند استفاده میشود.
- نوع III: یک سیمان با مقاومت زودرس بالا است که باعث میشود بتن سریع بچرخد و مقاومت کند. سیمان نوع III ازنظر شیمیایی و فیزیکی مشابه نوع I است با این تفاوت که ذرات ریز تر خردشدهاند.
- نوع IIIA: یک سیمان با مقاومت زودرس بالا است که برای بتن ریزی پروژههایی که نیاز به حفره هوادارند استفاده میشود.
- نوع IV: قدرت را با سرعت کمتری نسبت به انواع دیگر سیمان ایجاد میکند و در هنگام هیدراتاسیون گرمای کمتری تولید میکند. از آن برای سازههای بتونی با جرم بزرگ استفاده میشود که شانس کمی برای فرار گرما از آنها وجود دارد، مانند سدها.
- نوع V: فقط در سازههای بتونی که در معرض حمله شدید سولفاتها قرار میگیرند، بهطورمعمول در مکانهایی که بتن در معرض خاک و آبهای زیرزمینی با محتوای سولفات بالا است، استفاده میشود.
ASTM C-1157 شامل موارد زیر است:
- از سیمان هیدرولیک نوع GU برای ساخت عمومی استفاده میشود.
- نوع HE سیمان با مقاومت زودرس است.
- نوع MS نسبت به حمله سولفاتها مقاوم است.
- Type HS در برابر حمله سولفاتها بسیار مقاوم است.
- نوع MH در حین آبرسانی میزان متوسطی از گرما را تولید میکند.
- نوع LH در حین آبرسانی مقدار کم گرما تولید میکند. این نوع سیمان همچنین میتواند برای واکنشپذیری کم گزینه R با سنگدانههای واکنشپذیر قلیایی طراحی شود.
چه مواد مکملی برای تولید سیمان پرتلند استفاده میشود؟
پوزولان ها
مواد دیگر ممکن است باسیمان پرتلند مخلوط شود تا نیازهای خاص و ملاحظات زیستمحیطی را برآورده کند. برخی از این مواد که پوزولان نامیده میشوند تا زمانی که باسیمان پرتلند مخلوط نشوند، خاصیت سیمانی ندارند. هنگامیکه بتن برای بتن ریزی مخلوط میشود، برای بهبود کارایی و ویژگیهای جریان آن، آب بیشتری فراتر ازآنچه برای هیدراتاسیون موردنیاز است، اضافه میشود. این آب اضافی سپس در کانالهای مویرگی ریز در بتن هیدراته (سخت شده) وجود دارد.
هنگامیکه یک ماده پوزولان جای بخشی از سیمان را میگیرد، یک واکنش شیمیایی ثانویه پس از هیدراتاسیون اتفاق میافتد. مواد شیمیایی آزادشده از خمیر سیمان در طی هیدراتاسیون با مواد شیمیایی موجود در ماده پوزولان واکنش داده و مادهای را تشکیل میدهند که این کانالهای مویرگی را بهطور جزئی یا کامل پر میکند. این امر باعث متراکم شدن بتن و افزایش مقاومت آن در برابر مواد شیمیایی شده (مانند موادی که برای عملیات یخزدایی استفاده میشود) که میتواند به بتن متخلخل نفوذ کرده و فولاد تقویتکننده را خورده و باعث خراب شدن سطح و یا جوش خوردن آن شود.
وقتی بخشی از سیمان با پوزولان جایگزین شد، در حین هیدراتاسیون گرمای کمتری تولید میشود. این واکنش ثانویه مقداری گرما تولید میکند، اما دماپایین تر است و در مدتزمان طولانیتری پخش میشود. ازآنجاییکه بتن با خنک شدن منقبضشده (کاهش مییابد)، گرمای کمتر به معنی جمع شدگی کمتر است. ازآنجاکه انقباض باعث ایجاد تنشهایی میشود که با ترکخوردگی برطرف میشوند، جمع شدن کمتر به معنی ترکهای کمتر است. این امر بهویژه در سازههای با جرم زیاد که نمیتوانند بهراحتی گرما آزاد کنند، مانند سدها مهم است.
خاکستر بادی محصول جانبی صنعتی
خاکستر بادی یک محصول جانبی صنعتی است که گاهی بهعنوان جایگزینی جزئی برای سیمان پرتلند استفاده میشود. خاکستر بادی از ذرات غیرقابلاحتراق تشکیلشده که از گاز دودکش نیروگاههای زغالسنگ سوزانده حاصل میشوند. بسته به عملکرد موردنیاز بتن در بتن ریزی و نوع زغال سوخته، ممکن است تا ۶۵٪ از جرم مواد سیمانی تشکیل شود.
بازیابی خاکستر مگس برای مصارف صنعتی عملی کاملاً سازگار با محیطزیست است، زیرا خاکستر مگس از گاز دودکش خارج میشود تا کیفیت هوا بهبود یابد و استفاده از آن در سیمان به این معنی است که آنچه درگذشته ماده زائد بود اکنون بهعنوان یک ماده مفید بازیافت میشود.
برخی از حقایق مرتبط در مورد خاکستر بادی استفادهشده در بتن ریزی
خاکستر بادی در انواع F و C وجود دارد.
- خاکستر بادی نوع F با سوزاندن زغالسنگ سختتر و قدیمیتر ساخته میشود. اینیک پوزولان است و وقتی با آب مخلوط شود، ترکیبات سیمانی تولید نمیکند مگر اینکه مخلوط شامل سیمان پرتلند باشد.
- نوع C با سوزاندن زغال جوانتر و نرمتر ساختهشده و هنگامیکه با آب مخلوط میشود دارای برخی ترکیبات سیمانی است.
ذرات بسیار ریز خاکستر بادی میتوانند خصوصیات جریان بتن را بهبود بخشند، با جایگزینی سیمان هزینهها را کاهش دهند، به آب کمتری در مخلوط نیاز داشته و بتن را متراکم کنند. ذرات درشت مزایای یکسانی ندارند و ذرات درشت و ریز را نمیتوان همیشه بهطور مؤثر تفکیک کرد. همچنین ممکن است زمان تنظیم را افزایش دهد.
خاکستر بادی رنگدانهها یا لکههای اسید و همچنین سیمان را قبول نمیکند، بنابراین مطابقت با بتن موجود ساختهشده بدون خاکستر میتواند یک مشکل باشد. ویژگیهای عملکرد خاکستر بادی با اندازه ذرات متفاوت بوده، اما همچنین با ترکیب شیمیایی زغالسنگ، درجه پودر شدن زغالسنگ قبل از سوختن، شرایط احتراق در کوره و روشهای جمعآوری و کاربری خاکستر بادی متفاوت است.
ازآنجاکه این فاکتورها هرگز در نیروگاههای مختلف یکسان نیستند و حتی ممکن است باگذشت زمان در یک نیروگاه تغییر کنند، خواص خاکستر بادی میتواند بسیار متفاوت بوده که این میتواند مانعی برای کسب نتایج مداوم خوب باشد. خاکستر بادی دارای یک سطح خاص ۱۴۰۰ تا ۳۴۰۰ فوت مربع در پوند (۲۸۰ تا ۷۰۰ مترمربع در کیلوگرم)، بسته به نوع آن است.
خاکستر، سرباره کوره بلند
سرباره کوره بلند و دانهریز (GGBFS) یکی دیگر از محصولات جانبی صنعتی است که بعضاً بهعنوان جایگزینی جزئی برای سیمان پرتلند مورداستفاده قرار میگیرد GGBFS. یک ماده شیشهای و دانهای است که در کورههای بلند بهعنوان محصول جانبی از فرآیند ساخت آهن و فولاد تولید میشود. این نمونه دیگری از مادهای است که قبلاً بهعنوان زباله در نظر گرفته میشد اما امروزه بهخوبی در صنعت از آن استفاده میشود.
مزایای بتن ساختهشده برای بتن ریزی باسیمان پرتلند GGBFS
- آهستهتر سخت میشود.
- در هنگام هیدراتاسیون گرمای کمتری تولید میکند.
- برای مدت طولانیتری به قدرت خود ادامه میدهد.
- در بتن ریزی بتن بادوامتری تولید میکند.
دماهای پایین تولیدشده توسط GGBFS در طی هیدراتاسیون باعث میشود اتصالات کنترل، از هم دورتر شوند GGBFS 1. به باسیمان پرتلند جایگزین میشود و ممکن است تا ۷۰٪ از جرم مواد سیمانی تشکیل شود. سطح مخصوص GGBFS 1700 تا ۲۹۰۰ فوت مربع در پوند (۳۵۰ تا ۶۰۰ مترمربع در کیلوگرم) است.
موارد استفاده از بخار سیلیکا در بتن ریزی
از بخار سیلیس گاهی اوقات برای افزایش خصوصیات خاص بتن استفاده میشود. اینیک پودر بسیار ظریف و شبیه شیشه است که در طی مراحل تولید فلزات سیلیکون از گازهای دودکش کورههای قوس الکتریکی جمع میشود. قبل از اجرای قوانین سختگیرانه زیستمحیطی در اواسط دهه ۱۹۷۰، بخار سیلیس جمعآوری نمیشد. اکنون به یکی از باارزشترین و همهکاره مواد افزودنی بتن برای بتن ریزی در جهان تبدیلشده است.
برخلاف شن و ماسه ذرات بخار سیلیس محلول در آب هستند، به این معنی که آنها میتوانند بهعنوان بخشی از فرآیند هیدراتاسیون، واکنش شیمیایی نشان دهند. بخار سیلیس تقریباً ۱۰۰ برابر کوچکتر از ذرات سیمان پرتلند است و بنابراین اندازه کوچک آن، همراه با مقدار نسبتاً زیاد سیلیس، آن را به یک پوزولان بسیار واکنشپذیر تبدیل میکند.
اندازه ذرات کوچک آنها همچنین باعث میشود که بخار سیلیس بتواند فضاهای بین دانههای سیمان را پر کند که بستهبندی ذرات نامیده شده و باعث میشود بتن متراکمتر و کمتر متخلخل یا نفوذپذیر در برابر رطوبت باشد. همچنین مقاومت فشاری، مقاومت اتصال بین ذرات، سنگدانهها و فولاد تعبیهشده و مقاومت در برابر سایش را بهبود میبخشد.
بخار سیلیس ممکن است تا ۱۲٪ از جرم مواد سیمانی تشکیل شود. یکنواختی دود سیلیس با توجه به خصوصیات شیمیایی آلیاژهای فلزی ساختهشده، میتواند متفاوت باشد. بخار سیلیس از حداکثر چهار کوره مختلف گاهی اوقات باهم مخلوط میشود تا یک محصول یکنواختتر فراهم شود. اثرات روی تغییرات بتن در خصوصیات شیمیایی بخارات سیلیس از کورههای مختلف بهخوبی شناختهنشده است.
کاربرد نرمکنندهها در تولید بتن برای بتن ریزی
خصوصیات بتن بخار سیلیس نیز با خصوصیات و مقادیر مختلف و عوامل مختلف کاهشدهنده آب (نرمکنندهها) که بهطورمعمول هنگام افزودن بخار سیلیس به بتن برای بتن ریزی استفاده میشوند، متفاوت است. ازآنجاکه سطح عظیم دود سیلیس از آب بیشتری استفاده میکند و کارایی آن را کاهش میدهد، نرمکنندهها و فوق نرمکنندهها برای سیال شدن بتن به آن اضافه میشوند تا بتوان با آن کار کرد.
قبل از حمل بار به محل کار، بتن معمولاً در کارخانههای محلی مخلوط میشود. گیاهان دستهای معمولاً دارای سیلوهای حاوی خاکستر بادی بوده و اغلب دارای GGBFS در دست هستند. تسهیلات نگهداری دائمی بخار سیلیس کمتر معمول است.
مصالح بهکاررفته در بتن و مزایای آن
سنگدانهها مواد دانهای بوده که شامل؛ ماسه، شن، سنگ خردشده، سنگ رودخانه و سنگدانههای سبک تولیدشده هستند و ممکن است تا ۷۵٪ از حجم کل بتن را اشغال کنند. ازآنجاکه سنگدانهها از خمیر سیمان قیمت کمتری دارند، برای کمک به کاهش هزینهها به بتن اضافه میشوند. خصوصیات سنگدانهها میتواند تأثیر قابلتوجهی در کارایی بتن برای بتن ریزی در حالت پلاستیکی آن و همچنین دوام، مقاومت، چگالی و خصوصیات حرارتی بتن سخت شده داشته باشد.
سنگدانهها از کجا آمدهاند؟
سنگدانهها سنگین هستند. استخراج آنها در یک منطقه مرکزی و حملونقل آنها در مسافتهای طولانی هزینه زیادی ندارد، بنابراین سنگدانهها معمولاً بهصورت محلی استخراج میشوند. این بدان معنی است که بسته به زمینشناسی محلی، خواص معدنی، شیمیایی و فیزیکی احتمالاً در مناطق مختلف متفاوت است. مواد معدنی با خصوصیات مختلف میتوانند در مقابل فرآیندهای شیمیایی یا شرایط موجود در بتن واکنش متفاوتی نشان دهند، بنابراین سنگدانهها یکی دیگر از مواد تشکیلدهنده بتن برای بتن ریزی هستند که میتوانند خصوصیاتی متفاوت داشته باشند.
عملیات حفاری سنگ معدن
کل معادن سنگشکن مشابه مواردی است که در استخراج سنگ برای سیمان استفاده میشود. دکل حفاری در حال حفاری سوراخهایی است که در آن بارهای انفجاری ایجاد میشود، درحالیکه یک کامیون با سنگی کندهشده، سنگ را به سنگشکن شماره ۱ میرساند.
در معادن قدیمی بیشتر کارشده، بنابراین عمیقتر هستند. این عملیات در حفرههایی با عمق ۳۵ فوت، در مقابل ۸۰ فوت در معدن سنگآهک، انجام شد. در اینجا نیز انفجار توسط پیمانکار فرعی انجام میشود. این عملیات علاوه بر منطقه پردازش شامل چندین معدن سنگی بوده، بنابراین یک عملیات بزرگ است.
عملیات خرد کردن و مرتبسازی از یک برج کنترل مرکزی مشرفبه منطقه عملیات کنترل میشود. نوار نقاله نزدیکترین دوربین پس از پردازش توسط دستگاه سنگشکن شماره ۱ سنگ را جابجا میکند. گاهی دو دستگاه سنگشکن اضافی در نزدیکی مرکز قرار میدهند که باوجود خرد شدن، حمل، هل دادن و انداختن سنگ روی انبارها، گردوغبار موجود در هوا حداقل است.
تراکم و درجهبندی سنگدانه در خمیر سیمان
سنگدانه خوب درجهبندیشده، نتیجه استفاده از اندازههای مختلف سنگدانه در مخلوط است. این کمک میکند تا مقدار خمیر سیمان موردنیاز برای پر کردن فاصله یا خلأ بین قطعات جداگانه منفرد، کاهش یابد. کاهش درصد خمیر سیمان در مخلوط به کاهش جمع شدگی و کاهش حرارت هیدراتاسیون کمک میکند که هر دو میتوانند بتن را ترک کنند.
همچنین دوام آن را بهبود میبخشد. مقدار سنگدانه مورداستفاده در مخلوط را تراکم بستهبندی آن مینامند. سنگدانههای دارای درجهبندی خوب نسبت به سنگدانههای دارای درجه شکاف دارای تراکم بستهبندی بهتری هستند. سنگدانههای دارای درجهبندی شکاف فاقد قطعههایی با اندازه متوسط هستند که این امر باعث دشوارتر شدن محل بتن و افزایش هزینه آن میشود و هر دو عامل میتوانند بر محصول نهایی تأثیر بگذارند.
تأثیر منفی مقدار بیشازحد آب در بتن
به خاطر داشته باشید که مقدار بیشازحد آب میتواند با افزایش درصد ساختار مویرگی باقیمانده، بتن را ضعیف کند، زیرا آب اضافی با خروج به سطح خود راهیافته و سپس تبخیر میشود. حداکثر اندازه سنگدانه باید کمتر از یکپنجم باریکترین بعد بین اضلاع فرمها، یکسوم عمق دالها یا سهچهارم حداقل فاصله شفاف بین میلههای تقویتکننده باشد.
برای به حداقل رساندن مقدار سیمان موردنیاز و همچنین به حداقل رساندن جمع شدگی خشک شدن بتن، گاهی اوقات استفاده از بزرگترین اندازه سنگدانه ممکن توصیه میشود. عیب استفاده از سنگدانه درشت و بزرگ این است که احتمال خرابی پیوند بین سطح سنگدانه و خمیر سیمان اطراف را افزایش میدهد، زیرا تنشهای موجود در سطح مشترک بین دو ماده بیشتر از سنگدانه کوچکتر است. همچنین کل سطح پیوند سطحی موجود را کاهش میدهد.
ویژگیهای سفتی تغییر شکل سنگدانه نیز مهم است. اختلافات زیاد در خواص سنگدانه و خمیر سیمان باعث ایجاد تنشهای زیادی میشود که باعث ایجاد ترکهای ریز شده که میتواند بتن را ضعیف کند.
محتوای رطوبت و تأثیر آن در مخلوط بتن
انواع مختلف سنگدانهها دارای تخلخل متفاوت هستند؛ یعنی میتوانند مقادیر مختلف آب را جذب کنند. سنگ بسیار متخلخل بسته به اینکه اشباع از آب باشد یا خشک قبل از افزودن به مخلوط بتن، تأثیر متفاوت میگذارد. سنگ خشک آب بیشتری از مخلوط جذب میکند و این میتواند بتن را سخت و سختتر کند که ممکن است بهعنوان مشکلات قابلمشاهده در بتن تمامشده، ظاهر شود. هنگام محاسبه مقدار آب اضافهشده به مخلوط، آب موجود در سنگ اشباع باید در نظر گرفته شود یا ممکن است نسبت آب بیشازحد زیاد باشد، درنتیجه بتن ضعیف شود.
اندازه توده متراکم سنگدانه
سنگدانههای بتن برای بتن ریزی بهطورکلی به دودسته ریزودرشت تقسیم میشوند. سنگدانههای ریز بهطورکلی شن و ماسه طبیعی یا سنگ خردشده هستند و بیشتر ذرات از غربال ۳/۸ اینچی (۹.۵ میلیمتر) عبور میکنند. دانههای درشت بهطورکلی بین ۳/۸ تا ۱-۲/۱ اینچ (۹.۵ میلیمتر تا ۳۷.۵ میلیمتر) قطر دارند. بیشتر سنگدانه درشتی که در بتن استفاده میشود سنگ خردشده هستند، اگرچه از سنگ رودخانه صاف نیز استفاده میشود.
مقدار ناکافی از سنگدانههای ریز میتواند باعث مشکلات در پمپاژ بتن و مشکلات در دستیابی به سطوح صاف مالهای شود. مقاومت پیوند سنگدانههای ریز تحت تأثیر شکل یا بافت سنگدانه قرار نمیگیرد، زیرا ذرات کوچکتر مقدار زیادی از سطح را ارائه میدهند که در آن اتصال به خمیر سیمان میتواند انجام شود. خصوصیات سطحی سنگدانه ریز میتواند بر میزان آب موردنیاز برای کار کردن بتن تأثیر بگذارد.
چهار سطح مختلف رطوبت
- آون خشک (OD) به معنی از بین بردن تمام رطوبت است.
- خشک شدن هوا (AD) به این معنی است که رطوبت سطح برطرف شده و منافذ داخلی تا حدی پرشدهاند.
- سطح اشباعشده از سطح خشک (SSD) به این معنی است که رطوبت سطح برطرف شده و تمام منافذ داخلی آن پر است.
- مرطوب به معنای پر شدن منافذ است.
از بین این چهار حالت، سطح اشباع و خشک، بهترین حالت رطوبت در نظر گرفته میشود. در SSD، سنگدانه در حالت تعادل قرار دارد، بنابراین سنگدانه با جذب آب، آن را به خمیر سیمان نمیدهد. بااینحال، به دست آوردن این حالت رطوبت ممکن است دشوار باشد.
تسهیلاتی برای تولید سنگدانههای سبک (مصالح سبک)
سنگدانههای سبک بهطورمعمول ساخته دست بشر بوده و بسیار متخلخل هستند. رس، شیل و تختهسنگ وقتی گرم شوند، کمی شبیه پاپ کورن گسترش مییابند. ازآنجاکه بیشتر آنها متخلخل بوده، همچنین جذبکننده رطوبت هستند، میتواند بر مقدار آب مورداستفاده در مخلوط تأثیر بگذارد. چند نوع از سنگدانهها در طول فرآیند همجوشی، پوششی ایجاد میکنند که خاصیت جذب آنها را کاهش میدهد.
بااینحال، اگر این پوشش در حین جابجایی آسیب ببیند، کل ماده دانهای توانایی جذب آب را بازیابی میکند. بسته به درصد سنگدانهای که به پوشش آسیبدیده رسیده است، در صورت عدم مجاز بودن چنین تغییر در طراحی مخلوط، این شرایط میتواند بر کیفیت بتن در بتن ریزی تأثیر بگذارد.
سنگدانههای سنگینوزن (مصالح سنگین)
سنگدانههای سنگینوزن معمولاً در ساختمانهایی که به محافظت در برابر تشعشع نیاز دارند، استفاده میشوند و بیشتر بازرسان نگرانکننده نیستند.
مواد زائد بهصورت توده متراکم
بسیاری از ایدهها برای استفاده مجدد از مواد زائد در نظر گرفتهشده و برخی نیز امتحان شدهاند. بازرسان ممکن است با مشکلات ناشی از مواد نامناسب جایگزین سنگدانهها با بتن روبرو شوند.
برخی از این مواد زائد عبارتاند از:
- آوار ساختمانی
- زباله صنعتی
- باطلههای معدن
واکنش کل قلیایی (AAR)
برخی از انواع مواد سنگدانه با مواد قلیایی از منابع موجود در بتن برای بتن ریزی یا از منابع دیگر مانند؛ نمکهای یخزدایی، آبهای زیرزمینی یا آب دریا واکنش بدی نشان میدهند. اگر سنگدانهها حاوی درصد زیادی سیلیس باشند، واکنش را واکنش قلیایی-سیلیس (ASR) مینامند. اگر سنگدانه از سنگهای کربنات دولومیتی تشکیلشده باشد، به آن واکنش قلیایی-کربنات (ACR) میگویند.
در طول ASR که رایجتر است، سیلیس محلول در کل با قلیایی محلول واکنش میدهد و یک ژل قلیایی سیلیس تولید میکند. وقتی این ژل رطوبت را جذب کرد، منبسطشده و باعث ترک خوردن بتن میشود. بعد از قرار دادن بتن ممکن است مدتی طول بکشد تا ASR ظاهر شود.
ترک های درزهای کنترلی، ترکهای انقباضی یا میکرو ترکهای سطح که در اثر یخزدگی بزرگ میشوند، ممکن است باعث ورود رطوبت به بتن و جذب ژل شود. برخی از سنگدانهها غیر واکنشپذیر و برخی دیگر با درجات مختلف واکنشپذیر هستند. هیچ روش مقرونبهصرفهای برای کاهش بتن آسیبدیده توسط AAR وجود ندارد. اصلاح نیاز به حذف و جایگزینی دارد.
سایر مشکلات مرتبط با توده متراکم در بتن ریزی
- برخی از انواع سنگهای مورداستفاده برای سنگدانهها ممکن است با انبساط و انقباض در چرخههای ذوب به دلیل محتوای رطوبت، مشکلاتی را ایجاد کنند.
- سنگدانهها میتوانند ازنظر مقاومت در برابر سایش متفاوت باشند که می تواند در بتن ریزی ایجاد مشکل کند.
- ناخالصیهای کل متشکل از ذرات ریز و جامد میتوانند در پیوند سطح بین سیمان و سنگدانه درشت تداخل ایجاد کنند.
- ناخالصیهای کل محلول ممکن است ازنظر شیمیایی با خمیر سیمان قلیایی تداخل داشته باشد و بر زمانگیرش تأثیر بگذارد.
- برای جلوگیری از آلودگی نمکی که ممکن است ازنظر شیمیایی روی بتن تأثیر بگذارد یا به فولاد تعبیهشده حمله کند، باید مصالح سنگ معدن در مکانهای ساحلی تمیز شود.
بازرسان همیشه قادر نخواهند بود مشکلاتی را که مشاهده میکنند به مواد تشکیلدهنده خاص نسبت دهند. وقت گذاشتن برای یادگیری در مورد انواع مواد اولیه مورداستفاده در منطقه آنها و مشکلات معمول مربوط به این مواد، ممکن است به بازرسان کمک کند تا از اهمیت نقصهای مختلفی که کشف میکنند، بهتر درک کرده تا بتوانند توصیههای مناسب را ارائه دهند.
منظور از بتن پلیمری چیست؟
به کلی بتن های پلیمری شامل؛ ۸۰ الی ۹۵ درصد مواد پرکننده معدنی و گاهی مواد آلی و تنها ۵ الی ۲۰ درصد محلول مونومر برای ایجاد خواص پلیمری با آن ترکیب می شود.
برای اینکه بتوان یک بتن پلیمری با کیفیت تهیه کرد باید به نکات زیر دقت شود:
استفاده از بایندر مناسب
استفاده از نوع و میزان مناسب مواد پرکننده
استفاده از افزودنی های مناسب که خواص بتن را بهبود می بخشد.
روش ساخت بتن پلیمری
با در نظر گرفتن این موارد و تغییر صحیح آن ها برای کاربردهای متفاوت می توان انواع بتن پلیمری را با خواص دینامیکی، شیمیایی، فیزیکی، مکانیکی و حتی الکترکی متفاوتی ساخت. درحالی که به هیچ وجه نمی توان این کار را برای بتن های سیمانی انجام داد. درحال حاضر سه نوع بتن های پلیمری با نام های آپوکسی، پلی استر و پلی یورتان بیشترین کاربرد و میزان تولید را در حوزه ساخت و ساز دارند. ازجمله پرکننده های رایج برای ساخت این بتن ها نیز می توان به سیلیس و کربنات کلسم اشاره کرد.
بر اساس نتایج برخی آزمایشات روی انواع بتن پلیمری می توان از نتایج زیر نیز در ساخت این نوع بتن ها استفاده کرد:
بتن های پلیمری آپوکسی و پلی استر اصطکاک بالاتری دارند.
بتن های پلیمری پلی یورتان توانایی افزایش طولی زیادی دارند.
ساختار و کاربرد بتن پلاستیکی
مزایای استفاده از بتن پلاستیکی در بتن ریزی
نکات مهمی که مهندس ناظر قبل از بتن ریزی سقف باید کنترل کند!
باید قبل از بتن ریزی بعضی از موارد را چک کرد، در غیر این صورت بعداََ دچار خسارت و مشکل می شوید.
این موارد شامل:
۱. کنترل جک هایی که زیر تیر ها زده شده و خیز منفی که به تیر ها داده می شود.
۲. کنترل قالب بندی سقف
۳. کنترل قالب ها و گوه ها که در همه جا محکم فیت شده باشد.
۴. درزی توی سقف وجود نداشته باشد که موقع بتن ریزی شیره بتن بیرون نزند.
۵. به بالای سقف رفته که چک کنی قالب ها روغن خورده یا نه و اگر نخورده روی آن ها پلاستیک کشیده شده یا خیر.
۶. اسپیسر به اندازه کافی گذاشته شده یا خیر.
۷. کنترل تعداد آرماتور های سراسری تیر مطابق نقشه
۸. کنترل فاصله آرماتور های طولی از هم
۹. کنترل رعایت فاصله بینابینی خاموت های تیر
۱۰. کنترل اجرای اولین خاموت تیر بر ستونه (طبق آیین نامه، حداکثر ۶ سانتی متراست.)
۱۱. کنترل خیز سقف تیرچه بلوک
۱۲. کنترل عدم وجود شن، ماسه، فوم و غیره در قالب ها
۱۳. کنترل اجرای ادکا برای تیرچه
ضوابط ویژه اجرای بتن در هوای سرد
هوای سرد به وضعیتی اطلاق می گردد که برای سه روز متوالی، هر دوی شرایط (الف) و (ب) برقرار باشد:
الف) دمای متوسط روزانه هوا در شبانه روز کمتر از ۵ درجه سلسیوس باشد. منظور از دمای متوسط روزانه، میانگین حداکثر و حداقل دمای هوا در فاصله زمانی نیمه شب تا نیمه روز است.
ب) دمای هوا برای بیشتر از نصف روز از ۱۰ درجه سلسیوس زیادتر نباشد.
بتن ریزی در هوای سرد
بتن ریزی در هوای سرد به مواردی اطلاق می شود که بتن در دمای محیطی کمتر از ۵ درجه سلسیوس ریخته و نگه داری می شود. در این موارد باید تمهیدات خاص، هم برای ریختن و هم برای عمل آوردن، به کار گرفته شوند؛ تا از شرایط یخ زدگی جلوگیری شده و شرایط مناسب برای کسب مقاومت مطلوب تامین شوند.
اجرای بتن ریزی در هوای سرد
وقتی هوا سرد است، آب بتن یخ می زند و عملیات هیدراتاسیون سیمان کامل انجام نمی شود. از طرفی اگر آب یخ بزند باعث افزایش حجم بتن شده و ایجاد ترک می کند. پس حدالامکان در سرما بتن ریزی نکنید. موعی که باران و یا برف می آید بتن ریزی نکنید، چراکه باران می تواند سیمان بتن را بشوید همچنین آب اضافی که باران ایجاد می کندروی نسبت آب به سیمان بتن ما تاثیر منفی بگذارد مخصوصاََ که باران اسیدی باشد.
وقتی به ناچار بتن ریزی در هوای سرد انجام شود از ضد یخ استفاده می شود. ضد یخ در واقع یک افزودنیه که چند عملکرده است مثلاََ؛ هم روان کننده، هم گیرکننده و غیره است. ضد یخ باید کمتر از ۵ صدم درصد سیمان استفاده شده و حتما طبق دستور العمل شرکت سازندش استفاده شود. در مورد درصد اختلاط ضد یخ و بتن با خود شرکت سازنده صحبت کنیم که بعداََ به مشکل بر نخوریم.
ضد یخ و افزودنی های دیگر حکم دارو را دارند پس به دلیل عوارضی که بر جای می گزارند بهتره کمتر مصرف شود و همیشه در کنار ضد یخ چند مورد وجود دارد که می توانیم از آن ها استفاده کنیم.
فرق زودگیر (ضد یخ) بتن با زودگیر (ضد یخ) ملات چیست؟
۳ راه برای تشخیص وجود یون کلر در زودگیر بتن
بتن ریزی سقف در هوای سرد
آشنایی با انواع افزودنی های بتن
۳. کارایی کندگیر کننده ها در بتن ریزی
آثار نامطلوب هوای گرم بر بتن در بتن ریزی
آثار نامطلوب هوای گرم بر بتن تازه
آثار نامطلوب هوای گرم در بتن در حالت سخت شده
عوامل مهم در تسریع خسارات ناشی از هوای گرم
دمای استاندارد بتن برای بتن ریزی چند درجه است؟
برای طراحی داخلی، طراحی نقشه و طراحی نما ساختمان می توانید سفارش خود را به صورت آنلاین در سایت ما ثبت کنید!